Superior tank cleaning for the toughest debris and residues
Engineered for tank truck washes and other tough industrial applications, the GJ 18 provides high-impact cleaning for large industrial tanks.
The robust nature of the GJ 18 allows it to withstand demanding applications that require high temperatures and high concentrations of chemicals in the wash fluid.
Benefits:
- Longer uptime: Existing tank cleaners last 800-1000 hours before maintenance is required. The GJ 18 will run twice as long before needing service.
- Longer product life: The GJ 18’s patented over-sized “cartridge style” gear train is proven to last at least five times the wear time versus other tank cleaners.
- Lower maintenance costs: Costs to replace minor kits in the GJ 18 are 70-75% less than for other tank cleaners. Major kit replacements will cost 35-40% less.
- Simple to install: The pressure and flow of the GJ 18 match those of existing tank cleaners, so minimal adjustments are needed for installation.
- Easy to maintain: The GJ 18 has fewer individual parts than existing tank cleaners, meaning repairs are typically limited to normal wear parts and no special tools are required for service.
Lubricant . . . . . . . . . . . . . . . . . . . Food grade
Max. throw length . . . . . . . . . . . . . 100ft.
Pressure
Working pressure . . . . . . . . . . . . . . 45-300 PSI
Recommended pressure . . . . . . . . 50-200 PSI
Cleaning Pattern
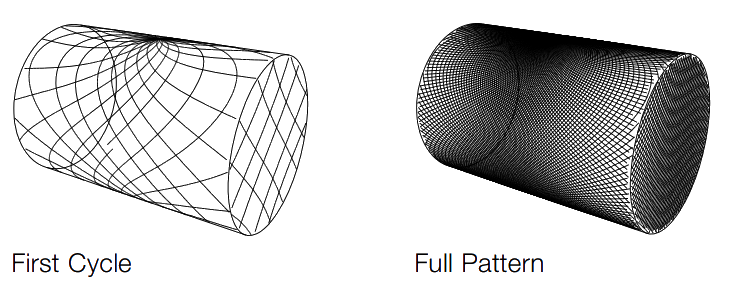
The above drawings show the cleaning pattern achieved on a cylindrical horizontal vessel. The difference between the first cycle and the full pattern represents the number of additional cycles available to increase the density of the cleaning.
Materials
1.4404 (316L), PPS, FKM (FFKM available)
Temperature
Max. working temperature . . . . . . . . 95°C (203°F)
Max. ambient temperature . . . . . . . . 140°C (284°F)
Weight . . . . . . . . . . . . . . . . . . . . . 26 lbs.
Connections
Standard thread . . . . . . . . . . . . . . . 2½” NPT, 2½” BSP
Caution
Avoid hydraulic shock, hard and abrasive particles in the cleaning liquid, as this can cause increased wear and/or damage of internal mechanisms. In general, a filter in the supply line is recommended. Do not use for gas evacuation or air dispersion. For steaming, we refer to the manual.